Back to Learning Resources
Problem solving with the '5 Why 1 How' technique
5 Why technique
Tags:
(5) Why – (1) How …. is a simple tool which addresses single-problem issues rather than complex broad organisational issues. It attempts to analyse a problem or issue by asking a series of “Why (did this happen)?” questions followed up by an attempt at addressing the Root Cause of the issue by asking (1) How (do we fix this problem once & for all?”).
The technique was originally developed by the Toyota Motor Corporation and is an important technique for problem solving.
The architect of the Toyota Production System, Taiichi Ohno, described the 5 whys method as “… the basis of Toyota’s scientific approach … by repeating why five times, the nature of the problem as well as its solution becomes clear.”
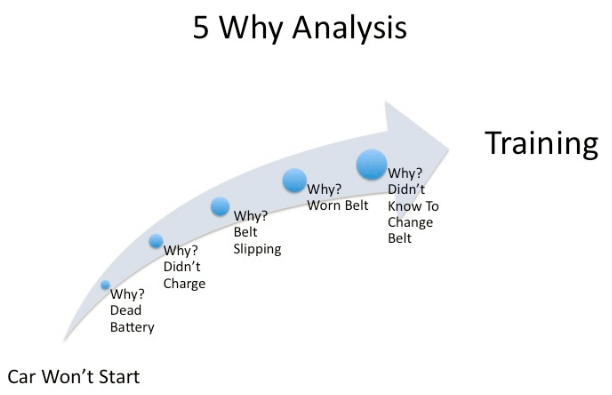
Example:
(1st Why) Why is there oil on the floor under the press?
A quick look found that the main return hose was leaking.
(2nd Why) Why is oil leaking from this hose?
After further investigation it was found that the hose is rubbing on a fan belt and had worn through.
(3rd Why) Why is it rubbing on the fan belt?
More investigation found that the fan belt housing was loose.
(4th Why) Why is the fan belt housing so loose?
After another check we found some of the bolts that hold the housing in place are not fully tensioned.
(5th Why) Why then are these bolts loose?
Nobody had serviced the press for over six months. (This is clearly the ROOT CAUSE of the problem.)
(1) How – How do we fix the problem?
Typically, this answer is a mixture of Immediate Corrective Actions:
Replace the hose and fan belt
Remove broken bolts on fan belt housing and replace with new ones
Torque all bolts to proper specifications, and
Preventive Action(s)
Check bolt torque regularly
Introduce a documented, preventive maintenance programme
Monitor the maintenance programme for effectiveness
Our example in this instance included (5) whys. The number of why’s is much less important than finding and fixing the root cause of the problem at hand.