Back to Learning Resources
Process Improvement - 5S
5S is a process improvement tool that seeks to improve the efficiency and flow of work. Sort, Straighten, Sweep, Standardise, Sustain
Tags:
5S is a process improvement technique named after the five steps, all beginning with 's'. Originally in Japanese (seiri, seiton, seiso, seiketsu, and shitsuke), the steps have been translated into five english 's' words: sort, straighten, shine, standardise, sustain.
Essentially the technique is to clean and organise your workspace to improve your workflow, and then to make this "the way it is done".
This video shows how 5S improves efficiency - Click here to view video
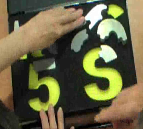
from https://www.leangames.co.uk/
Sort
The first task is to sort everything in the work area so that unnecessary items (tools, parts, equipment, storage bins, etc) can be removed and either discarded or stored elsewhere. This step de-clutters the workspace and prioritises tools and materials that are used frequently.
Straighten (Set in order or Systemise)
Then you arrange everything in the work area so that the work flows in an orderly fashion. This often involves creating storage solutions that facilitate the work flow, by placing more frequently used items so they are quick and easy to access. This step is usually about a workstation but can also include rearranging process steps to improve work flow on a larger scale.
Shine (or Sweep)
Depending on the starting state, this may involve a big initial effort, and can include painting and installing better lighting to make the workspace clean and tidy. Apart from resulting in a more pleasant and safer work environment, it will also be much easier to notice leaks, spills, breakages, etc.
However, 'shine' is also an important part of the ongoing process where the work space and equipment are cleaned and restored to their proper place at the end of each shift. Basic preventative maintenance tasks like tightening, oiling, restocking are part of this. The workstation is then ready for the next user (or the next day) and the order created in the first two steps is preserved.
Standardize
So that the 5S project is not just a spring cleaning exercise, you will need to ensure that everyone knows what are the current steps to follow and to establish expectations for the process.
In order for the changes to 'stick', you will need to conduct training, create documented procedures, work instructions, use visual guides, checklists, and/or photos. It will be easier to make changes if users of the system understand why they were made and ideally, they will have been involved in making the changes in the first place.
Visual controls include the familiar tape markings and shadow boards. By assigning everything to specific locations, you reduce time wasted looking for tools or equipment. If good visual controls have been installed, it should be immediately obvious if a problem exists in the work area, e.g. a missing tool.
Where there are multiple workstations for the same or similar tasks, setting them up in a standard way will increase efficiency and make them much more interchangeable for users.
Sustain
You have to keep it going so that the old ways do not return, otherwise all that time and effort and money will have been wasted. You will need to followup over a period of time until the 'new way' becomes entrenched.
This will be easier if the changes have made it easy to do the right thing. The design of the work should facilitate the process, not place a burden on employees.
Sustaining the new processes is often the most difficult task. If the focus drifts away from 5S, then the work area will drift back to the old state. Strategies include daily meetings, 'mini-audits', and ongoing continuous improvement efforts.