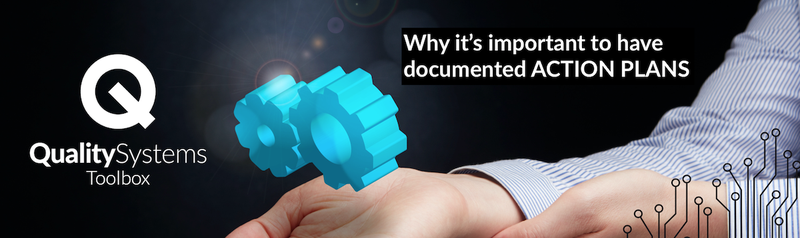
Regular shop floor meetings to discuss quality and safety issues are crucial in a manufacturing environment, just like Toolbox Talks in a construction work environment. It's a chance to go over the plan for the day and identify upcoming challenges or potential issues, so they can be addressed by working as a team to develop solutions.
These meetings provide a platform for employees to voice their concerns and ideas, and are a common way for businesses to meet the WHS legislative requirement for consultation in matters affecting worker health and safety.
To avoid meetings turning into a talkfest of hot air and no action, it's important to capture any tasks raised at these meetings in the form of an ACTION PLAN, assigning each task and setting a due date for completion. Someone must followup on the Action Plan at the next meeting (and/or in between) to make sure those tasks have been completed.
If you don't write down the tasks and who is responsible, they'll get forgotten. If there's no follow up on completion dates, then clearly they weren't important to management so the message that get's through is don't bother completing them. Pretty soon it will all feel a bit pointless, the regular meetings will fall by the wayside, and you've lost an important communication tool.
To make the meetings effective, you need to both write down the tasks AND do the follow up.
Regular reinforcement creates accountability and ensures that the tasks are completed in a timely manner. With the knowledge that the next meeting will start with a review of those tasks, I'm going to make sure mine is not the only task not done! Documenting the tasks also provides a record of progress, which can be useful in identifying trends or recurring issues.
If your action plan is managed in a spreadsheet or in the meeting minutes, then typically one person spends a lot of time doing reminders and progress updates and more reminders. With the tasks tracked in Quality Systems Toolbox, reminders are automated and tasks pop up on your work list. Everyone can see what needs to be done and hold each other accountable.
Regular meetings also help to establish a culture of safety in the workplace. Use the opportunity to review progress and key learnings from safety incidents captured in Quality Systems Toolbox. For any new issues or hazards or concerns raised in the meeting, enter them directly into the software where everyone can see what's happening. By prioritising safety and quality, employees are more likely to report any issues or hazards that they observe, knowing that something will be done. This will ultimately lead to a safer and more efficient workplace.
Meetings can also help to improve communication and collaboration between teams. By bringing together individuals from different departments or areas of expertise, opportunities for cross-functional collaboration can arise. This can lead to innovative ideas and solutions that may not have been possible otherwise.
But nothing will happen with those innovative ideas and solutions unless you put them in a written action plan and make sure to follow it up.