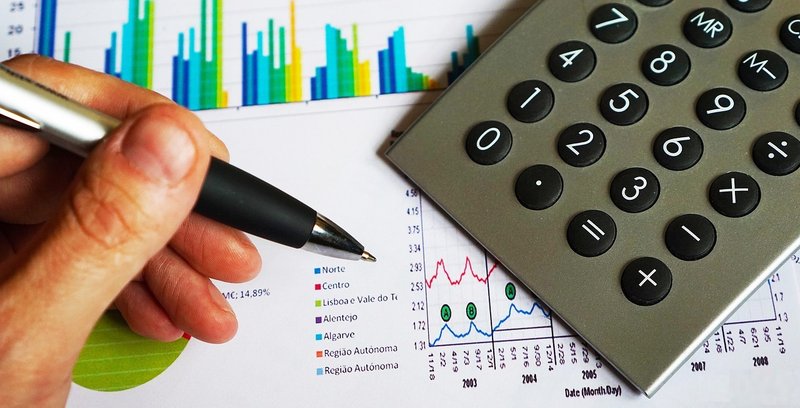
Monitoring the effectiveness of a Quality Management System (QMS) is used to assess the degree to which quality objectives are being met, and to identify areas for improvement. So what is a KPI, and how is it relevant to a quality management system and to business goals?
Understanding KPIs
A Key Performance Indicator (KPI) is a measurable value demonstrating how effectively an organisation achieves its key business objectives. In the context of a quality management system, KPIs are used to monitor, analyse, and improve the efficiency and quality of processes.
A good KPI provides impartial and clear information to track progress toward an end goal and to measure performance over time. The purpose of a KPI is to help management make data-driven decisions that will help the organisation grow and succeed.
Choosing KPIs Relevant to a QMS
First, decide on your objectives - what is important for your business to achieve - and then choose KPIs to match. Quality objectives relate to customer satisfaction and conformity of your product or service, so the KPIs chosen should provide some measure of those aspects.
For example, on-time delivery is something that customers care about, so it's a common quality objective for a manufacturing company. A matching KPI for this objective could be the percentage of deliveries that arrived on time. If shipping is not in your control or arrival data is hard to collect, then deliveries sent on time might be a better KPI. By monitoring this KPI monthly, the company will know how well the quality system is working and can quickly determine when a process needs fixing.
When choosing and defining KPIs, you must also decide how often to collect the data and who should be responsible for recording it.
Managing and Using Your KPIs
For a small business with only a few KPIs collected by the same person, it’s probably easy enough to manage KPI data in a spreadsheet. However, it gets complicated for larger organisations when different people report multiple KPIs on different frequencies.
Management system software like Quality Systems Toolbox can help you manage quality objectives and KPIs.
In QS Toolbox, each KPI can be assigned to the person responsible, and reminders can be sent according to the frequency at which you want the data reported. KPI data is stored in records, which can hold supporting material in attached files, such as the raw data or a detailed report. QSToolbox collates the KPI data in an exported “KPI report” to make it easy to review performance across multiple KPIs.
By tracking key performance indicators (KPIs), such as customer satisfaction levels, defect rates, on-time delivery performance, and internal process efficiency, the company can gain valuable insights into the effectiveness of its QMS.
Benefits of Using KPIs in QMS
KPIs provide a comprehensive view of how well the QMS functions and where improvements may be needed to achieve your short and long term goals.
Here are some example KPIs for a manufacturing company and the insight provided by each metric:
- Customer Satisfaction Index (CSI): Measure customer satisfaction through surveys, feedback, and complaints to assess whether the QMS meets customer expectations and delivers quality products.
- On-Time Delivery (OTD): Track the percentage of orders delivered on time to ensure that production and delivery processes are efficient and meet customer deadlines.
- First Pass Yield (FPY): Calculate the percentage of products that pass all quality checks on the first attempt, indicating the efficiency and effectiveness of the manufacturing processes.
- Defect Rate: Monitor the percentage of defective products or parts, identifying areas for improvement in manufacturing processes and quality control.
- Scrap Rate: Measure the percentage of material wasted during manufacturing to reduce waste and improve efficiency.
- Non-Conformance Rate: Track the percentage of products or processes that deviate from specified quality standards, enabling the identification of areas for corrective actions.
- Rework Rate: Measure the percentage of products that require rework due to quality issues, aiming to reduce rework and improve production efficiency.
- Supplier Performance: Evaluate suppliers' performance based on the quality of materials and components they provide and their ability to meet delivery schedules, as their performance directly impacts the overall product quality.
- Employee Training and Competency: Monitor the percentage of employees trained and competent in QMS processes, demonstrating a commitment to continuous improvement and adherence to quality standards.
- Audit Results and Compliance: Assess the results of internal and external audits, compliance with quality standards, and the effectiveness of corrective actions implemented.
- Process Efficiency and Cycle Time: Track manufacturing processes' efficiency and cycle time, aiming for improvements for continual improvement and reduced lead times.
- Management Review Effectiveness: Evaluate the outcomes and actions resulting from management reviews, ensuring that decisions lead to improvements in the QMS.
Using KPIs to Drive Continuous Improvement
Consistently monitoring and analysing your key performance indicators, such as production efficiency, product quality, and customer satisfaction metrics, will foster continual enhancement.
Using these KPIs to leverage the insights from this data will help you and your team members make well-informed business performance decisions through your quality management system.
Would you like to see how Quality Systems Toolbox software could help you? Please contact us to book your free demo or call us at 1300 551 588 (AET).