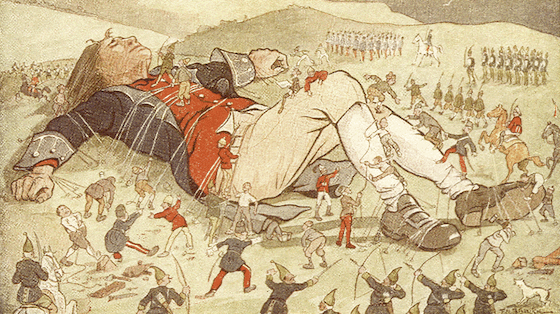
A nonconformity (or ‘nonconformance’) occurs when something does not meet the requirements in some way. Here’s more on nonconformance and ISO 9001
According to the ISO 9001 standard, something either conforms, or does not conform. There is no ‘in-between’ – no grading of nonconformity.
However, for many businesses there are good reasons to do so. The primary reason being that you want to make sure that you spend your time and money solving the important problems.
How do we determine what is ‘Major’ and what is ‘Minor’?
To a certain extent, you get to decide this yourself so that the definition is appropriate to your business.
For example, a hotel chain might decide that forgetting the chocolate on the pillow is a minor issue, but forgetting to change the sheets is major. This aligns with the service they provide as well as customer expectations.
A manufacturer producing high numbers of items will not action every defective product. The definition of major vs. minor will involve a threshold. For example, under 10 defective items per shift per machine is minor, and over this threshold is classed as major. The threshold will reflect the value of the items and depends on the product, the process step, the type of defect, and how much loss the company is willing to absorb.
For a plumbing or electrician business, invoicing errors like failing to invoice the customer for all the parts & consumables used on the job might be a minor or major non-conformance. It will depend on the amount, and also the degree to which the amount is recoverable.
Repeated minor mistakes can add up to significant losses in revenue, and would be classed as a major problem.
Here’s a guide for determining whether something is minor or major:
Minor:
- the problem is an isolated occurrence
- the problem does not affect the customer
- it creates little or no waste
- the defect can be rectified quickly/easily/cheaply
Major:
- delays that affect the customer’s schedule
- major delays to your delivery schedule
- rework, repeat service calls, or repairs
- the rejection of incoming goods or materials
- the rejection of a batch of finished product
- cost overruns (which result from all other failures), or cost surprises
- repeated occurrences of the same minor issue
When defining major/minor issues, you should also think about the downstream consequences of a nonconformity, i.e. a risk approach.
However, your don’t always get to decide:
A nonconformity against regulatory requirements is always major and must be addressed.
Keeping records
ISO 9001 and related standards require the business to keep records of nonconformities and the actions taken to address them. In QSToolbox, this is done via the Issue Tracker
If you do decide to treat minor nonconformities differently, you must still keep records on them. A repeating minor issue indicates a major problem, so you need records to be able to identify when minor issues recur. The system you use can be very “light” compared to the system used for dealing with major issues.
For example, the manufacturer above may use simple tally sheets for each machine to keep track of minor nonconformities. A mechanical workshop could use a logbook to collect the details of all minor problems. Field workers could report issues via a phone app, or email to a designated ‘issues’ address.
It is important to periodically review these records!
Work out a frequency to suit your business, and the kinds of minor issues you deal with. Then schedule and assign the regular review - in Quality Systems Toolbox.