Jan. 7, 2025
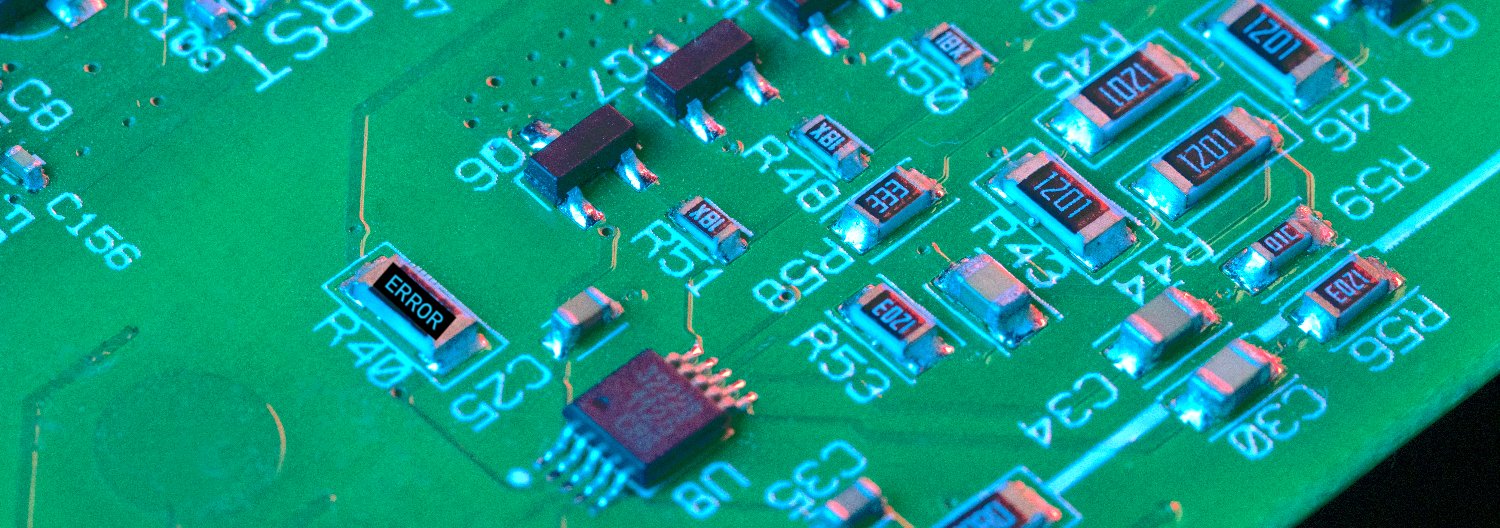
This story happened a few years ago. It involved a mid-sized manufacturer of complex waste-water monitoring equipment. They'd worked closely with a range of local and overseas clients to produce monitoring equipment and had a reputation for precision and reliability.
Manufacturing the devices was routine - until it wasn't.
An Undetected Error
The manufacturer received a shipment of components from their trusted supplier and proceeded with the standard assembly process.
However the supplied components did not meet specifications. The circuit boards being manufactured were never going to work with these components, but the problem went undetected.
No red flags were raised during the initial visual inspection prior to assembly and production continued smoothly for hundreds of boards.
The Devastating Discovery
A final, comprehensive functional test conducted at the end of production revealed that the entire batch of assembled boards would have to be scrapped.
The implications were profound and multi-faceted:
- Financial Loss: The entire production batch became scrap, representing a total loss of the materials and the labour costs, amounting to many thousands of dollars. There were also additional expenses for rush re-manufacturing and expedited shipping to avoid further losses from contract penalties.
- Reputation Damage: The company missed the delivery deadlines by several weeks and lost the trust and confidence of their customer. There were uncomfortable conversations to explain and justify significant production delays.
- Operational Disruption: The production line was shutdown and engineering resources diverted to troubleshooting the problem. Everything else had to be rescheduled because of the shutdown and to accommodate manufacture of replacements for the faulty boards. Subsequent production was put under pressure to catch up the lost time.
Investigating the Problem
The investigation revealed the fault in the components from the supplier, but this was really just the surface problem. They needed to keeping digging and ask another "why" to find out why faulty goods had been used in production.
The root cause of the issue was that the existing process for incoming goods inspection was not sufficient. It didn't address the risk of bad components. The same problem could easily happen again with another of their many products.
Implementing Corrective Actions
To address the root cause, the company implemented a multi-step inspection process for incoming components to verify that important specifications had been met before goods were used. The implementation included comprehensive in-house training for staff and detailed documented Inspection and Test Plans for components and assemblies, to standardise and control the quality inspection process.
They also established a process and clear procedures for addressing non-conformity so that employees would know exactly what to do if something wasn't right.
Further actions were taken to improve supplier management through documented quality agreements with key suppliers and regular supplier audits.
Finally, to limit losses in the event of any future production problems, the company implemented a first-off testing regime to detect faults at the beginning of the batch production rather than the end.
How Quality Systems Toolbox software helped
All of the new Inspection and Test Plan (ITP) documents created for all the different types of incoming goods were uploaded and managed with QSToolbox software for document control. New ITPs and all revisions go through an approvals process and versions are controlled.
The company used the 'Issues' module in QSToolbox software to implement a robust system for tracking non-conformance and corrective actions.
Employee training in the new process was recorded in the 'Training' module of QSToolbox software.
Supplier management is handled in the 'Contacts' module with scheduling of supplier audits, tracking results, and other supplier records.
A Good Result
Although it was painful, the company learned from the experience by following a process for investigating non-conformance and by targeting corrective actions at process improvements. They've eliminated that risk and ended up with a stronger business.
If instead they'd only replaced the faulty boards and moved on quickly to the next production batch, they'd have missed the improvement opportunity, learned nothing, and no doubt would have gone through the same experience again.
The Bottom Line
A well-documented and consistently applied incoming goods inspection process that is based on relevant risks is not a 'nice-to-have', it's a necessity. The costs of a robust inspection process are insignificant in comparison to the potential losses from faulty incoming goods.
In this case study it was bad components for an electronics manufacturer, but the same cautionary tale applies to many other goods and many other industries.
Image by freepik