Dec. 10, 2021
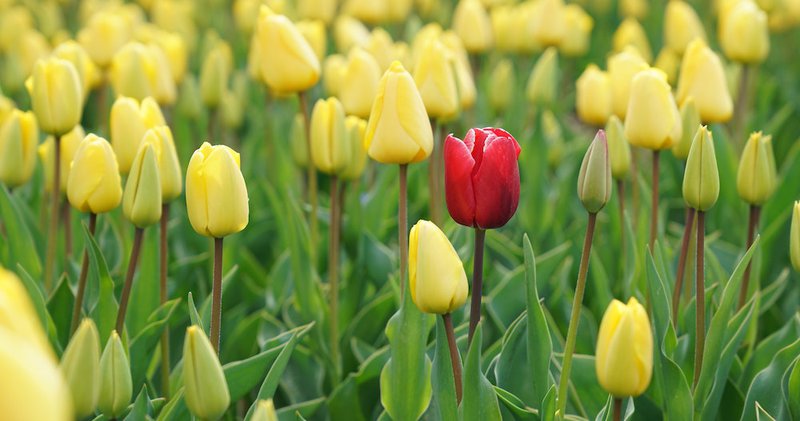
Go on say it...... quality control issues are a pain! They will not go away on their own and you are going to have to deal with them. If you don't know how to control them, or you delay fixing the problems you could be causing your company more pain and losses than you realize.
In this blog, Ian shows you exactly how to solve quality control problems, taking you step by step through the process we have developed over many years to ensure that your quality issues don’t become too big to handle, and will allow you to sleep peacefully at night!
And the cool part? This simple 6-step process we use is part of the workflow we have hard-wired into Quality Systems Toolbox.
Quality control and other types of issues are managed in the Issues module. You can read more about 'nonconformance' and 'corrective action' in our support resources.
With Quality Systems Toolbox you do not have to think, "What do I need to do next?" - just follow the process.
Here we go.....
1. Describe the issue
Include as much detail as you need to fully explain the problem. Do not apportion blame! This process is all about improvement. Add dates, times, locations etc: Add images when possible. Attach any documents/forms, as required. Note: Assign someone to be responsible to complete the next stage of the process. The person responsible can be changed at each stage of the process, as required.
2. Containment
Containment is all about what you can do next to stop the issues from getting worse while you investigate root causes. It could be as simple as removing the product from operations and affixing a "Defect" label on it or placing the item in a "Hold" Area. Actions at this stage could also include notifying the customer of a possible delay!
3. Investigate
This investigation process can be as simple as a quick review of the work area or product involved or it good be a full-blown deep-dive investigation using one of the many problem-solving techniques, such as Root Cause Analysis or The Five Why's. Avoiding this investigation stage will not win you any kudos if you intend to gain Certification to one of the International Standards for Management Systems.
4. Propose
At this stage, you can propose one solution or provide details of a range of options for remedial treatment of the issue. Hint: Make sure any discussions are captured in notes. Costings of options may also be tabled at this stage.
5. Implement
Nearly there...once a decision has been made it's time to turn the action plan into reality and make the necessary changes. Remember to update any associated work instructions, tooling, and notify suppliers if they are involved.
6. Verify
Okay, so all the changes have been made. It is going to be necessary at some stage to review them to make sure everything has gone to plan and the original problem is fully resolved. It's probably best to allow a bit of time for the remedial actions to settle in before rushing in to verify complete satisfaction.
That's it. All done. Problems resolved!